About Our Technology
You cannot buy a higher quality riflescope
That’s a strong claim, without a doubt. But, it’s a claim we can prove. And our customers do prove it… every day, under some of the harshest, most unforgiving conditions on earth. We didn’t start building scopes and expect people to find uses for them. Instead, we looked at real-world needs. Needs that were not being met by other optics. And created, from the ground up, the ultimate precision instrument for the intended application. You can tell the difference the moment you pick one up. And if you could look inside a Nightforce scope, the differences would be even more obvious.
Our riflescopes are subjected to rigorous testing during product development to ensure they will function in the worst conditions. Pre-production riflescopes are pressure tested to 120 pounds per square inch (psi), which is equivalent to an underwater depth of over 275 feet. The construction is validated over a thermal shock cycle where the temperature is reduced to -40°F then raised rapidly over a one-hour period to 158 °F. The mechanical function of the riflescope is tested at these extreme temperatures. Finally, scopes are recoil tested in multiple axes at accelerations exceeding 1,250g.
Before it is shipped to a customer, every riflescope is completely inspected and checked at 70 to 130 different points, depending on the model. We perform a battery of tests, including forward impact, side impact, tracking accuracy and resolution integrity. These are but a few of the steps we take to ensure absolute quality before any riflescope leaves our facility.
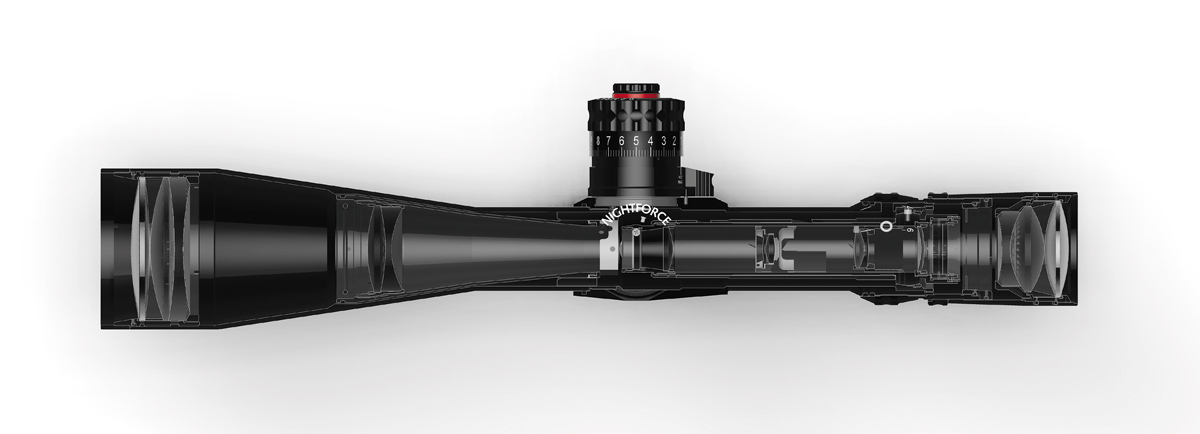
A scope’s objective lens determines resolution, light transmission and exit pupil size. To maximize these attributes, every Nightforce objective lens assembly utilizes a multi-element design like those found in the highest quality telescopes. Our lens system focuses light rays more precisely for exceptional image clarity and color accuracy.
All air-to-glass surfaces receive our proprietary broadband multi-coating; applied to tolerances of 1/4 wave deposition or .000005 inches, exceeding the toughest Mil-Spec abrasion test. You will see the difference in low-light situations.
Every lens in a Nightforce scope is matched and aligned by hand perfectly to its partners. This technique, called optical indexing, yields the highest possible optical performance. Because it takes time and considerable expertise, many manufacturers don’t bother. We’ve done it this way since the beginning.
Nightforce tubes are machined from solid bar stock 6061-T6 aircraft-grade aluminum alloy, not extruded or formed like those found on lesser scopes. They are two to three times thicker than other riflescopes. This means less overall stress, greater thermal stability, a consistent zero and a virtually impervious shield for the precision optics within.
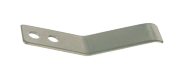
The spring that maintains pressure on our elevation and windage adjustments spends two weeks in a polishing tumbler before going into a Nightforce riflescope, to assure there are no rough spots or burrs to interfere with perfectly smooth operation. The NXS™ titanium spring has been optimized for a lifetime of performance, designed to never reach its fatigue limit or establish a memory, even if the setting is unchanged for long periods of time. This guarantees zero loss of integrity, zero loss of repeatability. It is many times more expensive than comparable springs found in most scopes. But, we are not concerned with a few dollars. We are concerned with building the best riflescope.
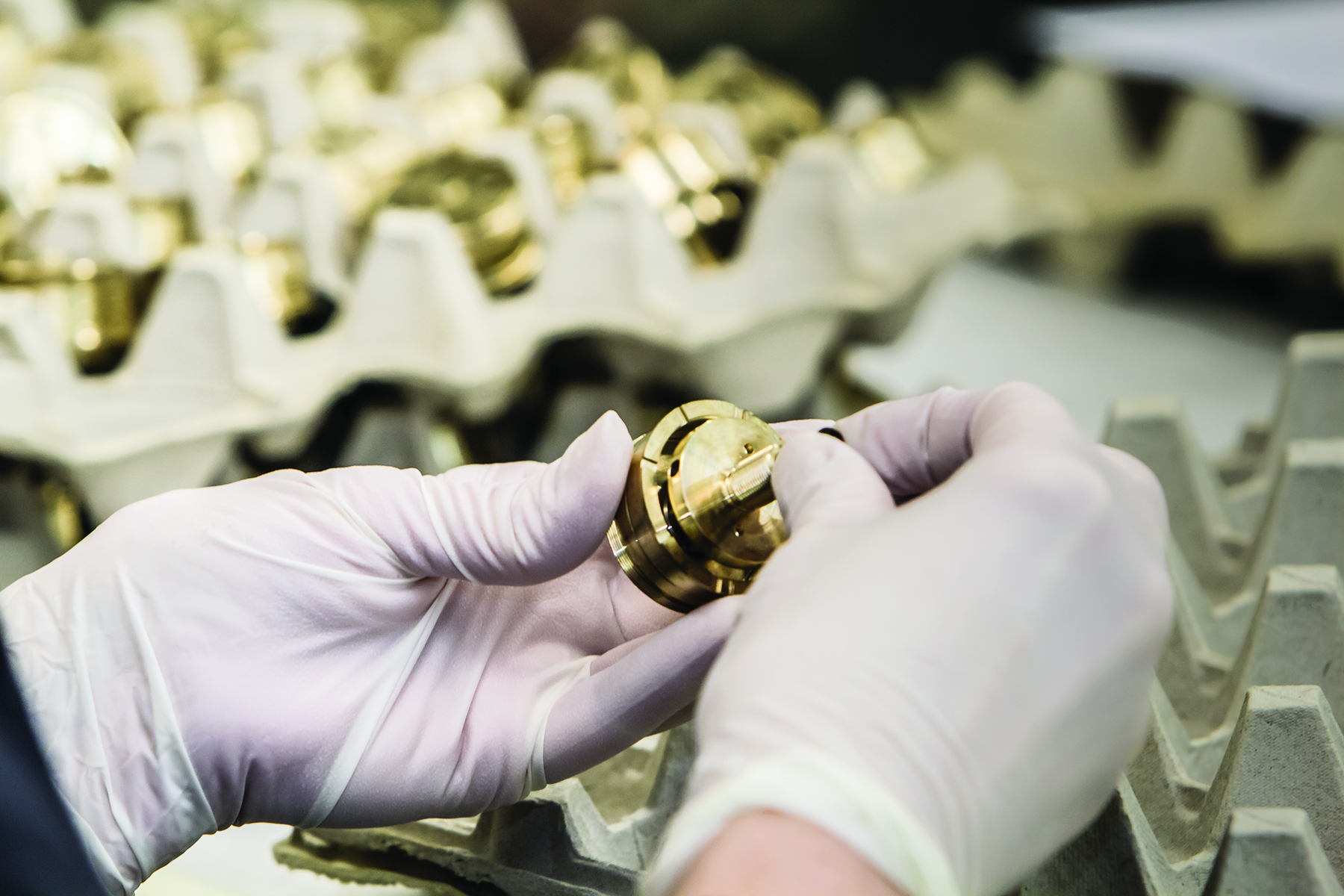
We machine the screw that controls elevation adjustments to an unbelievable 110 threads per inch. It is so precise that it must be mated to its receiver by hand. Why go to so much trouble? Because we consider backlash clearance of more than 1/30 the thickness of a human hair unacceptable.
Available with Nightforce ZeroStop technology that allows an absolute return to your chosen zero point, regardless of how much you have adjusted elevation settings.